
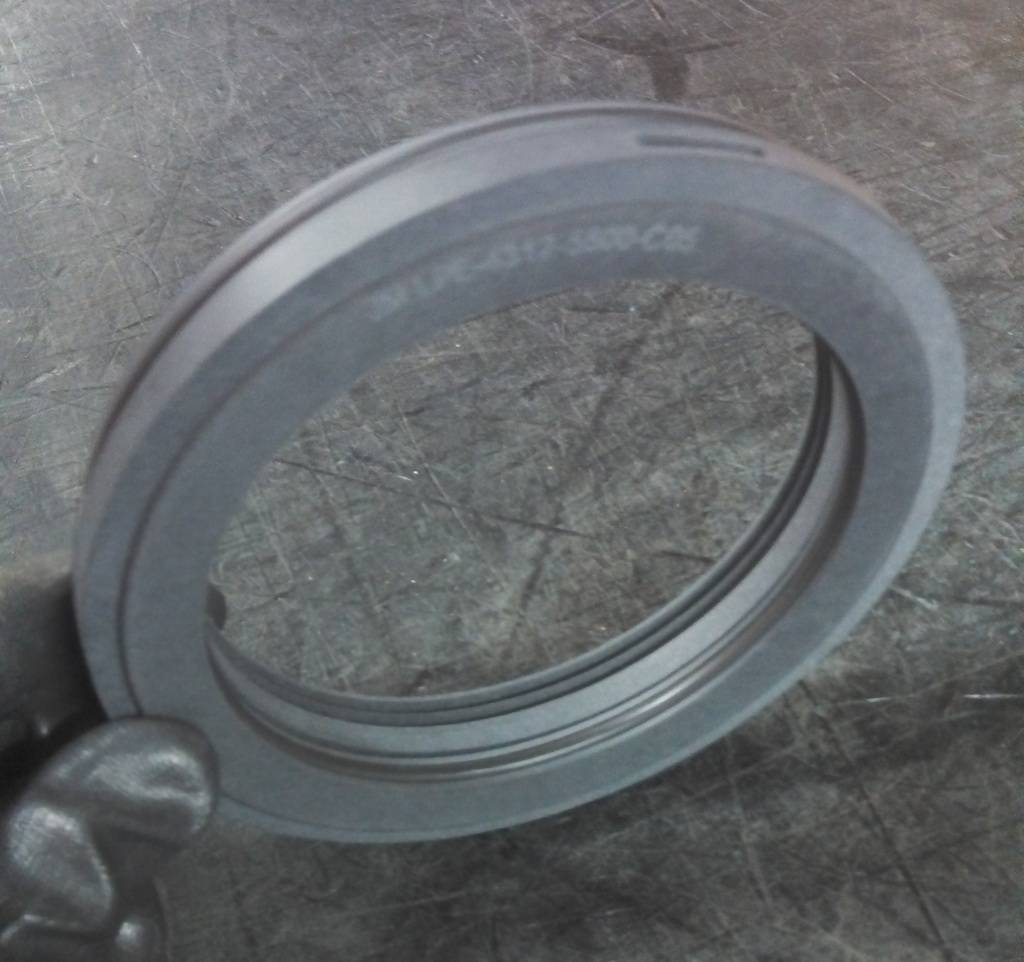
However, now comes patented technology from IsoMag that provides a positive seal with exceptional operating life (100,000 hours) and virtually no heat added to the bearing temperature.Īs the pioneers in the use of magnetic energy to advance bearing isolator technology, IsoMag continues to be on the forefront of innovation to continuously extend rotating equipment meantime between repair (MTBR).įor more information on IsoMag bearing isolator technology click here. As a consequence of these findings and in an effort to reduce the pressure-related alternating in-and-out flow of contaminated ambient air, conventional labyrinths are often replaced by rotating labyrinth seals, which are often called bearing isolators or bearing protectors, for short. Neither of these issues are factors for non-contacting bearing isolators. non-contacting has been with potential limits on operating life (wear of the seal faces) and heat generation due to the friction at the contacting seal faces.

The concern about using contacting IsoMag bearing isolators vs. Stand-by conditions – pumps and other rotating equipment Oil mist systems – pumps, motors and other rotating equipment Vertical installations – gearboxes, motors, pumps, mixers, agitators, etc. However, the positive seal provided by the contacting IsoMag bearing isolator provides superior performance in additional services such as:įorced circulation – pumps and steam turbines PTFE and metallic designs available in flanged and non-flanged designs to suit application requirements and various. In simple terms, a bearing isolator consists of a stationary component (stator) and a rotary component (rotor). The VBXX introduces the now-standard XX Interface to the Inpro/Seal Bearing Isolator design. Bearing isolator labyrinth seals are used to protect the bearings and bearing lubrication in rotating equipmentsuch as electric motors, gearboxes, pumps and split pillow block bearings. Orlowski then turned his attention to solving this issue on process pumps, where rubber lip seals were standard. ProTech bearing isolators are the leading technology in bearing protection with their unitized, two-piece design, providing zero lubricant leakage and total exclusion of contaminants. Orlowski and his team retrofitted the API refinery pumps with standard API labyrinth seals, made with a rotor and a stator.
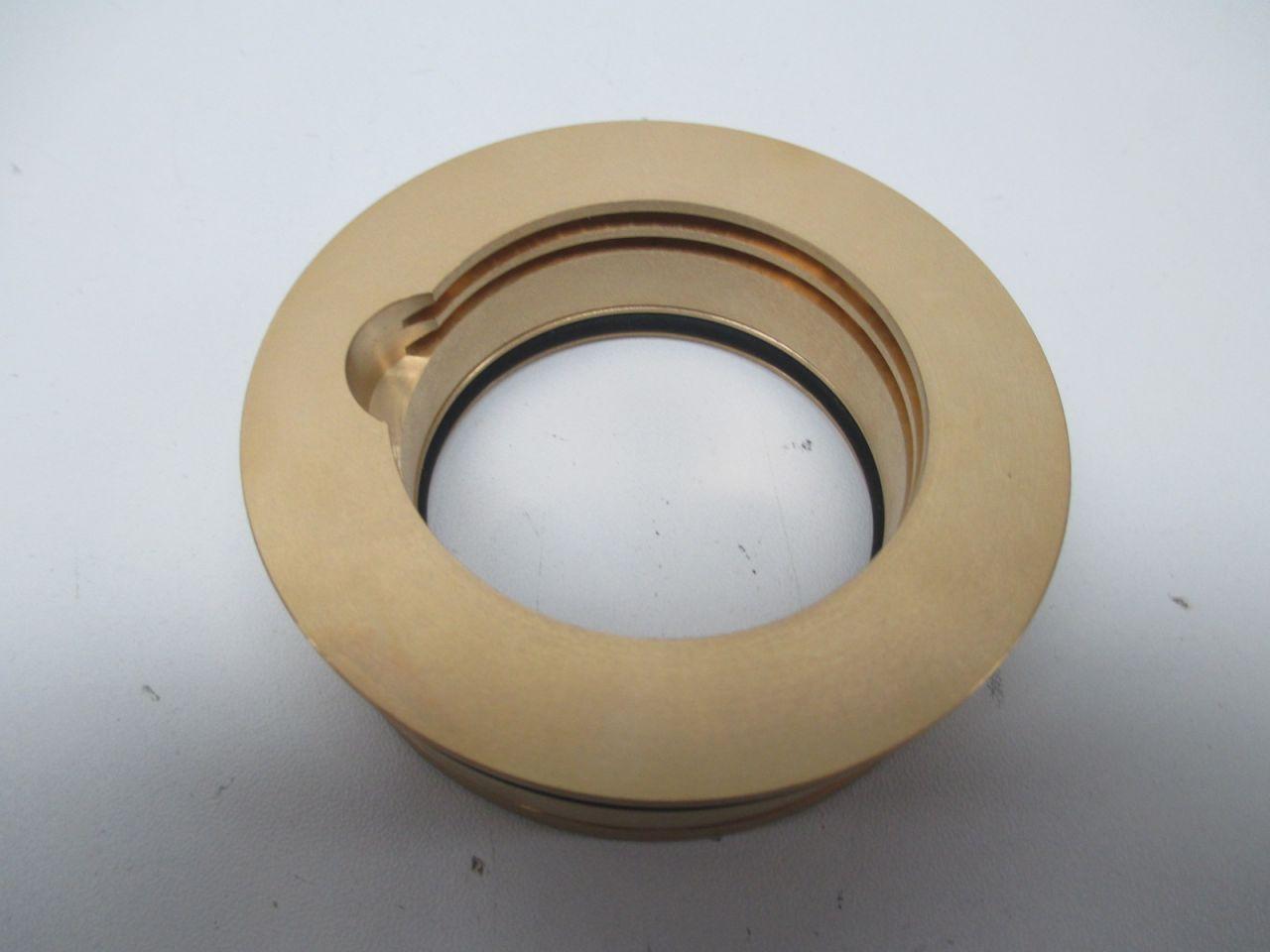
The non-contacting bearing isolator is a labyrinth device that relies on close clearances between a stationary and rotating component.īoth technologies work well in applications where the equipment shaft is horizontal and the bearing lubrication method is a bearing sump where the lubrication is “splashed” within the bearing housing. ProTech Bearing Isolator Labyrinth Seals. This led to innovation in the form of bearing isolators. As higher performing equipment was needed to survive harsher environments, so were better protections for the bearings. The contacting IsoMag bearing isolator is a positive sealing device with the seal face closing force provided by magnetic energy. Bearing isolators are a more recent development in seal technology, a protective measure to replace traditional seals on bearings within rotating equipment. The fundamental difference between the two technologies is: The two basic types of bearing isolators are contacting (positive seal) and non-contacting (labyrinth). The purpose of a bearing isolator is to prevent leakage of the bearing lubrication while also protecting the bearing lubrication from external contamination. No matter the size or complexity, Inpro/Seal® and PUMPNSEAL’S team can design a custom seal for your equipment.įor all Inpro/Seal® Bearing Protection enquiries please contact PUMPNSEAL on (08) 9302 8444.Bearing Isolators: Contacting vs.
Bearing isolator vs labyrinth seal full#
Outside contamination attempting to enter the bearing housing is captured in the outer labyrinth paths and expelled through a port in the stator by centrifugal force and gravityĪt PUMPNSEAL we offer full seal refurbishment for all manufacturers.Bearing lubricant is captured in the inner portion of the labyrinth and flows back to the bearing housing. Components of a bearing isolator with the labyrinth pathway highlighted in yellow Grease Purge Grease is an easy lubricant to apply and maintain, and it can be used to prevent contamination.The rotor and stator form a non-contact, compound labyrinth, so there is nothing to wear out. This two-part dynamic seal consists of a stator press-fitted into the bearing housing and a rotor attached to the shaft. Also find product list from verified suppliers. With the latest engineering and manufacturing technology Inpro/Seal® can meet your reliability requirements with seals designed specifically for your equipment with quick, timely deliveries. Bearing Isolator - Labyrinth Seals - Buy Labyrinth Seals at best price of Rs 2500/piece by Sealdyne Systems. Inpro/Seal® Bearing Isolators are made of high quality bronze and are designed to last for at least 100,000 hours compared to the common lip seals which usually fail after only 3,000 hours. The Inpro/Seal® Company manufactures a Bearing Isolator that will provide the highest level of bearing protection available.
